Preventing "Dieseling" in Hydraulic Cylinders
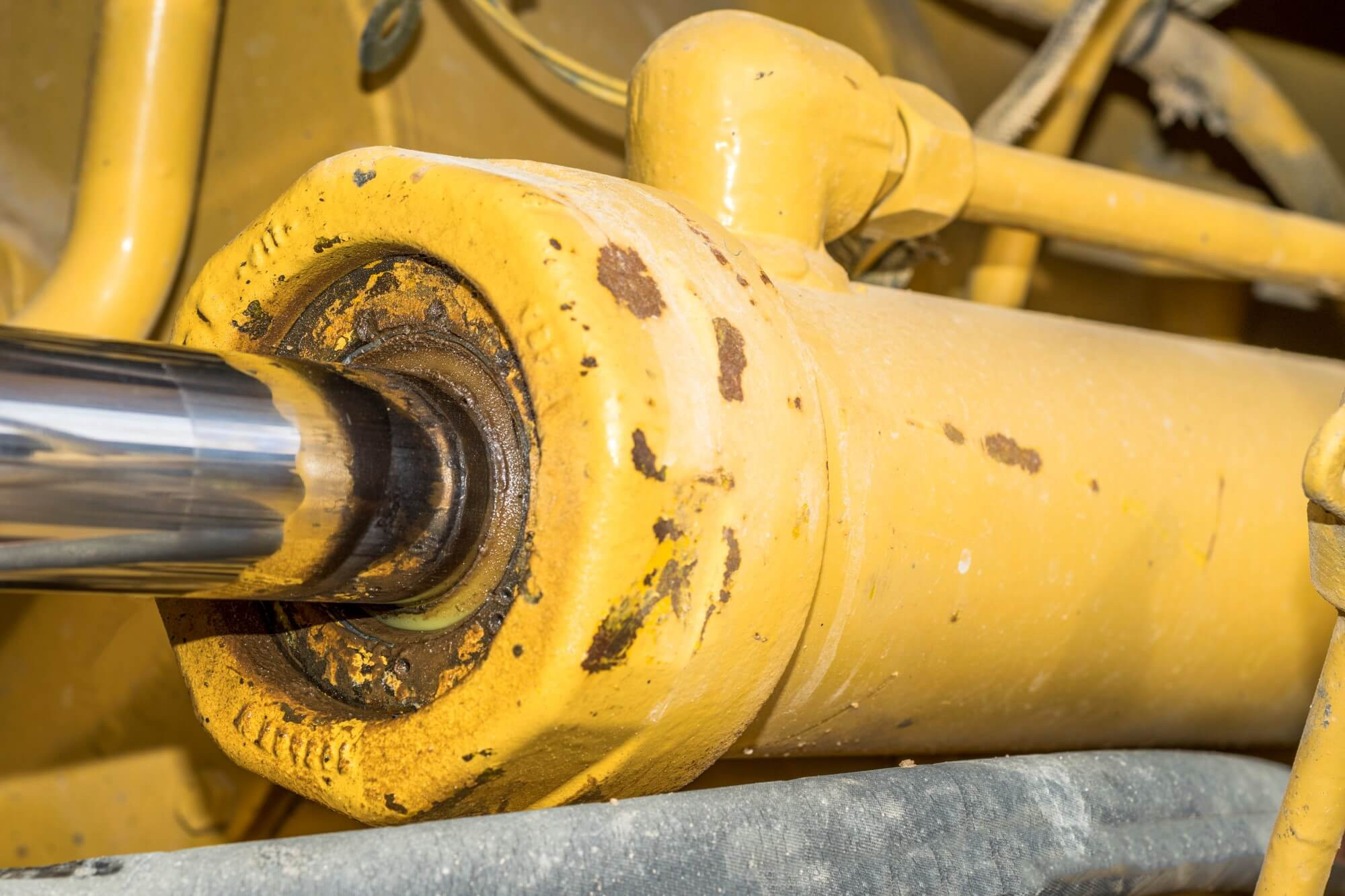
When air becomes mixed with hydraulic oil within cylinders, it sets the stage for a dangerous occurrence known as "hydraulic dieseling”.
This phenomenon occurs when air bubbles within the oil, undergo extreme pressure, leading them to explode, much like diesel fuel ignites within an engine cylinder. Bottom line is – it’s bad news. These little explosions rapidly deteriorate cylinder seals, causing hardening, cracking, and ultimately, seal failure. In this article, we look at the causes of hydraulic dieseling and how to prevent it.
Causes of Hydraulic Dieseling:
Hydraulic dieseling occurs primarily due to the presence of air in hydraulic fluid, which can enter the system through various avenues:
Air Introduction during Filling or Flushing: Failure to properly purge air from cylinder chambers during commissioning, filling, or flushing operations can introduce air into the system, increasing the likelihood of dieseling.
Air Bubbles Caused by Negative Pressure: Inadequately designed systems may draw air past cylinder rod seals during retraction, especially under negative pressure conditions, leading to the formation of air pockets.
Loose Hoses or Connectors: This is a big one! Leaks at connection points provide pathways for air to enter the hydraulic system.
Clogged Filters and Strainers: Obstructions within the hydraulic system, such as clogged filters, can cause pressure drops, reducing oil solubility and facilitating the formation of air bubbles.
Faulty Float Valves: Malfunctioning float valves can create negative pressure within the cylinder, allowing air to be drawn past rod seals.
Pump Inlet Problems: Leaks in suction lines or low reservoir oil levels, permit free air to enter the pump's inlet, becoming entrained air as it exits the pump and mixes with compressed oil.
Worn Hydraulic Pump Components: Wear in pump shaft seals and other components increases the likelihood of air ingress into the system.
How to prevent it:
To minimise the presence of air in hydraulic cylinders, i.e. dieseling, we need to address the faults, i.e. the reason why air is penetrating into the cylinder.
The following will help:
Pre-fill and Bleed the Hydraulic System: Prior to start-up, fill the cylinder with clean hydraulic fluid through service ports and purge air from the system by cycling the cylinder several times without load.
Regular Valve Inspection and Adjustment: Ensure valves are operating correctly and adjust them as necessary at prescribed intervals.
Scheduled Maintenance of Cylinder Components: Maintain all cylinder components through a scheduled preventative maintenance program to ensure optimal functionality. Flotek does these for many organisations.
Proper Cylinder Design: Ensure the cylinder is designed to meet your requirements, to minimise negative pressure events.
By adhering to correct commissioning and maintenance procedures, you can reduce the presence of air in hydraulic cylinders, and lower the risk of hydraulic dieseling. This underscores the importance of conducting thorough inspections, and repairs if you do have a leaky cylinder seal.
We’re the Hydraulic System experts - it’s our day job!
Addressing underlying dieseling issues is crucial to preventing bigger problems down the track. If you’re concerned about dieseling in your cylinders, you can call us on 9397 0044. We’ll have one of our Technicians to your site within 24 hours, anywhere in greater Melbourne to do a full inspection – which may not cost very much, but can save you $1000’s.
Our mission is to keep your production going – it’s all about More Up-Time.