Metro Tunnel Case Study
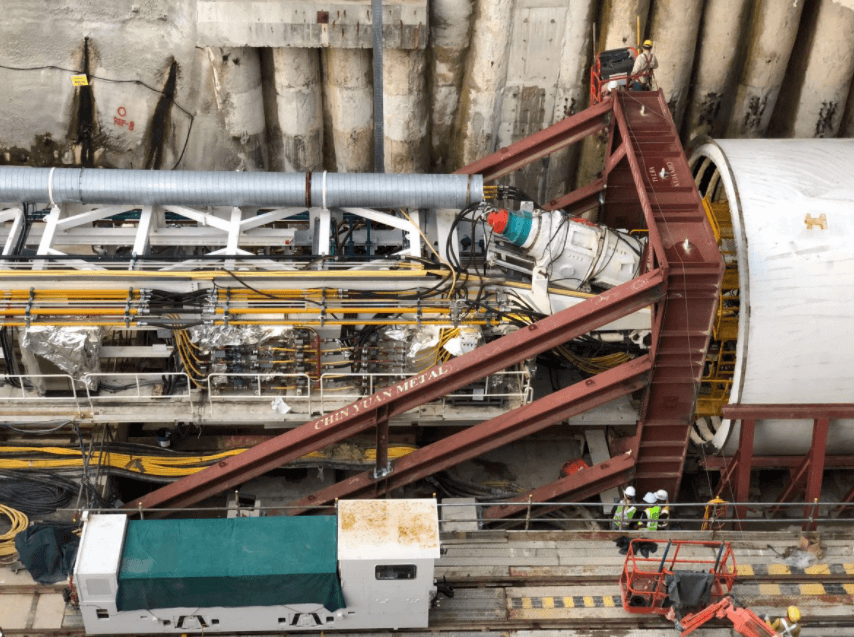
Q. How do you start boring a tunnel, when there’s nothing to push back against?
A. You can either have 1200 people stand behind the boring machine, or you can build a thrust frame for the machine to push back against as it starts drilling.
In 2019 when Melbourne’s Metro Tunnel Project was about to start drilling its first major tunnel, the huge boring machines needed something to push back against. A thrust frame, or push frame was built for this purpose.
However, the frame needed to be secured to the ground, as there are massive forces at play when a 350-ton boring machine starts drilling horizontally into the earth. In order to secure the thrust frame, huge custom-made reinforced WR-grade DSI steal thread bars, with unique threads were made. The question then becomes, how do you secure these bars tightly, given they have a custom-made thread?
To secure these bolts, which hold down the thrust frame, the bars need to be pulled up into extreme tension, as the nut is further tightened. Brett Blakemore (Flotek, Managing Director) said, “The bar tensioning is crucial in the early stages, as it holds down the main thrust frame used to push the tunnel boring machines' cylinders, to get the process started. Before the first part of the hole is created, there’s nothing to push against. Therefore, the bars holding down the thrust plate need to withstand an incredibly large force”.
Enerpac provided the equipment to do this tensioning, however, it’s not so easy when the steal thread bar has a custom-made thread. There needed to be something specifically designed, as there is no off-the-shelf product for tensioning custom-made DSI thread bar. This is where Flotek stepped in. Enerpac approached Flotek to create a solution.
“There’s no off-the-shelf solution for tensioning DSI threadbar, so we had to create one. Given the thread bar was unique, and there were massive forces at play, coming up with a solution to tension these bars took us around 2 weeks. It incorporated an Enerpac RCH603 hollow cylinder tensioner with spring return, with an Enerpac P392 pump.” Brett Blakemore
Brett explained, “The Enerpac RCH603 hollow plunger cylinder is ideally suited for this tensioning task, as it can safely and efficiently provide up to 567KN which is equivalent to around 65 tons of force, which is actually more than we needed.”
Before this solution could be used, it needed to be tested on-site. “The feedback from the Metro Tunnel Project site engineers has been very positive. The system is working exactly as intended, with no issues.”
This unique bolt tensioning tool created by Flotek, which is all about tensioning anchor points, or stud tensioning, has also been used on other Melbourne infrastructure projects such as the Westgate Bridge.
Flotek has used Enerpac products on most of Melbourne’s major infrastructure projects, including the North-East Link, the Westgate Tunnel Project, and the Metro Tunnel project. These included large hydraulic jacks, and synchronised hoists to move significant construction components. Brett explained, “Enerpac is a global leader with more than 50 years of experience. Because of this, their products are super-reliable, and the on-site service is great, which makes them easy to partner with on these types of ultra-important projects.”
About Flotek
Flotek has been Australia’s leading hydraulic service company for more than forty years. With a fleet of highly trained hydraulic technicians and a state-of-the-art cylinder repair facility in Melbourne, Flotek services heavy machinery, fixed plant equipment, and large construction hydraulics for some of Australia’s biggest companies. As the authorised distributor of both Enerpac and Hydac Hydraulic equipment, Flotek continues to work at the cutting edge of hydraulics in Australia.
24hrs per day, 7 days per week 9397 0044. We keep your business and projects moving.